Services
Whether you're addressing energy losses, upgrading system components, facing an unexpected breakdown, or maintaining the performance of mission-critical equipment, IAC is there for every stage of your compressed air system.
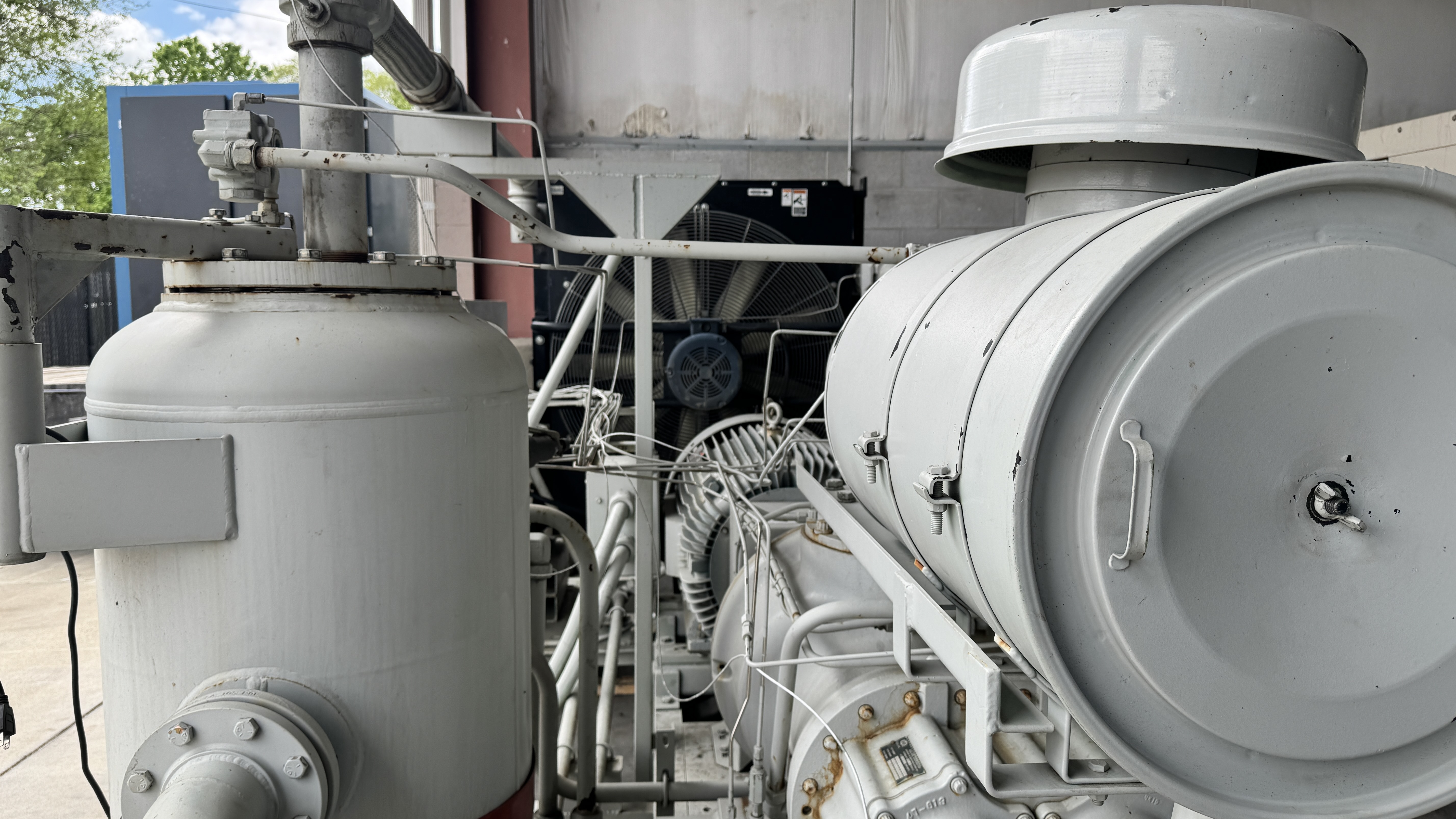
Custom Service Agreements
Unlike one-size-fits-all contracts, IAC offers five levels of standard service agreements—each customizable to fit your facility’s needs. Whether you need routine maintenance or full system support, IAC delivers coverage that aligns with your operations.
Compressed Air as a Utility (CAS)
CAS is IAC’s highest level of service—your compressed air system becomes a utility. We design, install, own, and maintain your equipment, while you receive clean, dry air billed monthly—just like electricity or water.